Synthetic Rubber: Composition & Uses - FUNAS
- What is Synthetic Rubber Made Of? FUNAS
- Understanding the Building Blocks of Synthetic Rubber
- Common Monomers in Synthetic Rubber Production
- The Polymerization Process: Creating Synthetic Rubber
- The Role of Additives and Fillers
- FUNAS's Utilization of Synthetic Rubber in Insulation Products
- Advantages of Synthetic Rubber Insulation
- Synthetic Rubber in Various Industries: A Wide Spectrum of Applications
- FUNAS: Your Trusted Partner for High-Quality Insulation Solutions
- FAQs
What is Synthetic Rubber Made Of? FUNAS
Understanding the Building Blocks of Synthetic Rubber
Synthetic rubber, a versatile material with properties closely resembling natural rubber, isn't derived from rubber trees. Instead, it's a polymer, a large molecule made by chemically linking smaller molecules called monomers. The specific monomers used dictate the final properties of the synthetic rubber, leading to a wide array of applications. This is where the question what is synthetic rubber made of? gets complex and fascinating. The exact composition varies greatly depending on the desired properties and end-use application.
Common Monomers in Synthetic Rubber Production
Several key monomers are used in synthetic rubber manufacturing. These monomers are carefully selected and combined to achieve specific characteristics like elasticity, strength, durability, and resistance to chemicals or temperature extremes. Understanding these building blocks is essential to appreciating the versatility of synthetic rubber.
1. Styrene: Often used in the creation of styrene-butadiene rubber (SBR), a common type of synthetic rubber. SBR offers a good balance of properties, making it suitable for many applications. The addition of styrene enhances the rubber's strength and rigidity compared to purely butadiene-based rubbers.
2. Butadiene: This is a crucial monomer in many synthetic rubbers, including SBR and polybutadiene rubber (BR). Butadiene contributes to the rubber's elasticity and flexibility. The ratio of butadiene to other monomers affects the final material's properties.
3. Isoprene: Isoprene is a key component in polyisoprene rubber, which closely mimics the structure of natural rubber. This results in a synthetic rubber with exceptional elasticity and resilience. Polyisoprene is often preferred in applications demanding high flexibility and elongation.
4. Chloroprene: This monomer forms neoprene, a type of synthetic rubber known for its exceptional resistance to oils, chemicals, and solvents. Neoprene is often utilized in applications where chemical resistance is paramount.
5. Nitrile (Acrylonitrile-Butadiene): This copolymer offers excellent resistance to oils and fuels, making it ideal for applications such as seals and gaskets in automotive and industrial settings. The presence of nitrile groups increases the rubber's polar character enhancing its oil resistance.
The Polymerization Process: Creating Synthetic Rubber
The monomers don't simply mix to form synthetic rubber. They undergo a process called polymerization. This involves initiating a chemical reaction that causes the monomers to link together, forming long chains – the polymer. The process is carefully controlled to ensure the desired molecular weight and structure of the synthetic rubber. Different polymerization techniques exist, each producing rubber with slightly different characteristics.
The polymerization method employed dictates various properties, like the molecular weight distribution and the presence of branching or crosslinking. Controlling these aspects is vital for fine-tuning the final product's characteristics.
The Role of Additives and Fillers
While the monomers form the backbone of synthetic rubber, additives and fillers significantly influence its final properties. These materials are blended into the polymer to enhance specific characteristics or reduce production costs.
Additives: These can include antioxidants to prevent degradation from oxidation, vulcanizing agents (like sulfur) to create cross-links and enhance strength, and plasticizers to improve flexibility.
Fillers: Fillers like carbon black or silica are added to improve strength, abrasion resistance, or other properties, while also potentially reducing the cost of the rubber compound. The type and amount of filler used are carefully selected to achieve the desired properties for the specific application.
FUNAS's Utilization of Synthetic Rubber in Insulation Products
FUNAS, a leading provider of thermal insulation materials, understands the significance of selecting the right type of synthetic rubber for its products. We leverage the unique properties of different synthetic rubbers to create high-performance insulation solutions for diverse industries. Our expert engineers carefully select the optimal monomer composition and additives to tailor the rubber's characteristics to meet the specific demands of each application.
For example, in applications requiring resistance to high temperatures and harsh chemicals, we might utilize a neoprene-based synthetic rubber. In other applications where elasticity and flexibility are paramount, a polyisoprene or SBR-based formulation might be more suitable.
Our commitment to quality ensures that only high-grade synthetic rubber from reputable suppliers is used in our products. We strictly adhere to international quality standards to deliver reliable and long-lasting insulation solutions to our customers globally.
Advantages of Synthetic Rubber Insulation
Synthetic rubbers offer a range of advantages that make them highly suitable for thermal insulation applications:
* Excellent flexibility and elasticity: This allows for easy installation and conformity to complex shapes.
* High resistance to chemicals and oils: This is particularly important in industries like petrochemicals and chemical processing.
* Good thermal insulation properties: Effective at preventing heat transfer, reducing energy consumption.
* Durability and long lifespan: Synthetic rubbers can withstand demanding conditions for extended periods.
* Cost-effectiveness: Synthetic rubbers offer a good balance of performance and affordability compared to some other insulation materials.
Synthetic Rubber in Various Industries: A Wide Spectrum of Applications
The versatility of synthetic rubber has resulted in its extensive use across numerous industries. The ability to tailor its properties through the choice of monomers, additives, and processing techniques enables its application in a vast range of scenarios.
* Automotive: Used in seals, gaskets, hoses, and other components requiring flexibility, durability, and resistance to oils and fuels.
* Construction: Used in roofing membranes, waterproofing systems, and other applications requiring weather resistance and durability.
* Aerospace: Used in seals, gaskets, and other critical components where reliability and resistance to extreme temperatures are crucial.
* Medical: Used in gloves, tubing, and other medical devices requiring biocompatibility and sterilizability.
FUNAS: Your Trusted Partner for High-Quality Insulation Solutions
FUNAS is committed to providing cutting-edge insulation solutions to diverse industries worldwide. Our expertise in utilizing synthetic rubber, coupled with our rigorous quality control processes and diverse certifications, ensures that our products meet the highest standards of performance and reliability. Our comprehensive range caters to various needs, offering customized solutions to meet specific project requirements. Contact us today to learn more about how FUNAS can support your insulation needs.
FAQs
Q: What are the main differences between natural and synthetic rubber?
A: Natural rubber is derived from rubber trees, while synthetic rubber is produced chemically. Synthetic rubbers offer greater control over properties and can be tailored to specific applications, while natural rubber might exhibit superior elasticity in some instances.
Q: Is synthetic rubber environmentally friendly?
A: The environmental impact of synthetic rubber depends on the specific type and manufacturing process. Some synthetic rubbers are more sustainable than others. FUNAS prioritizes environmentally friendly practices and adheres to ISO 14001 environmental management system standards.
Q: What is the lifespan of synthetic rubber insulation?
A: The lifespan varies based on the type of rubber, the application, and environmental conditions. However, synthetic rubber insulation products are known for their durability and longevity, often exceeding many years.
Q: How is synthetic rubber recycled?
A: Recycling synthetic rubber is challenging but increasingly possible. Methods include shredding and reprocessing into new products or using it as a fuel source. Sustainable practices are crucial, and research into efficient recycling methods continues.
Q: What certifications do FUNAS insulation products hold?
A: FUNAS products hold numerous certifications including CCC, CQC, CE, ROHS, CPR, UL, and FM, alongside ISO 9001 (quality management) and ISO 14001 (environmental management). These certifications demonstrate our commitment to quality and environmental responsibility.
Q: Does FUNAS offer custom solutions for synthetic rubber insulation?
A: Yes, FUNAS provides brand customization services to meet the specific needs of our customers. We work closely with clients to design and manufacture tailored insulation solutions. Contact us to discuss your requirements.
Is Glass a Thermal Conductor? Insights by FUNAS
Is Stone Wool Insulation Better Than Fiberglass? | FUNAS
Understanding Nitrile Rubber Price Trends with FUNAS
Enhance Efficiency with Thermal Conductive Insulators | FUNAS
FAQ
How do I choose the right insulation for my project?
Our team can help you choose the best material for heat insulation based on your specific needs, such as thermal resistance, acoustic properties, and environmental conditions.
What types of rubber foam insulation do you offer?
We offer a wide range of rubber foam insulation with different thicknesses and specifications. Thermal insulation material manufacturer FUNAS sleeves and sheets are suitable for different application scenarios.
service
What is your shipping and delivery process like?
We offer reliable logistics services for insulation material wholesale, both domestically and internationally. Our team ensures secure packaging, timely shipping, and real-time tracking so that your order reaches you in perfect condition and on schedule.
How does your technical support work?
Our technical support team is available to guide you through every stage of your project—from product selection and design to installation. We provide expert consultation to ensure that you get the best insulation solution for your needs and can assist with troubleshooting if needed.
What types of rubber foam insulation products do you offer?
We offer a wide range of rubber foam insulation products, including custom shapes and sizes, thermal and acoustic insulation solutions, and options with specialized coatings such as flame retardancy and water resistance. Our products are suitable for applications in HVAC, automotive, construction, and more.
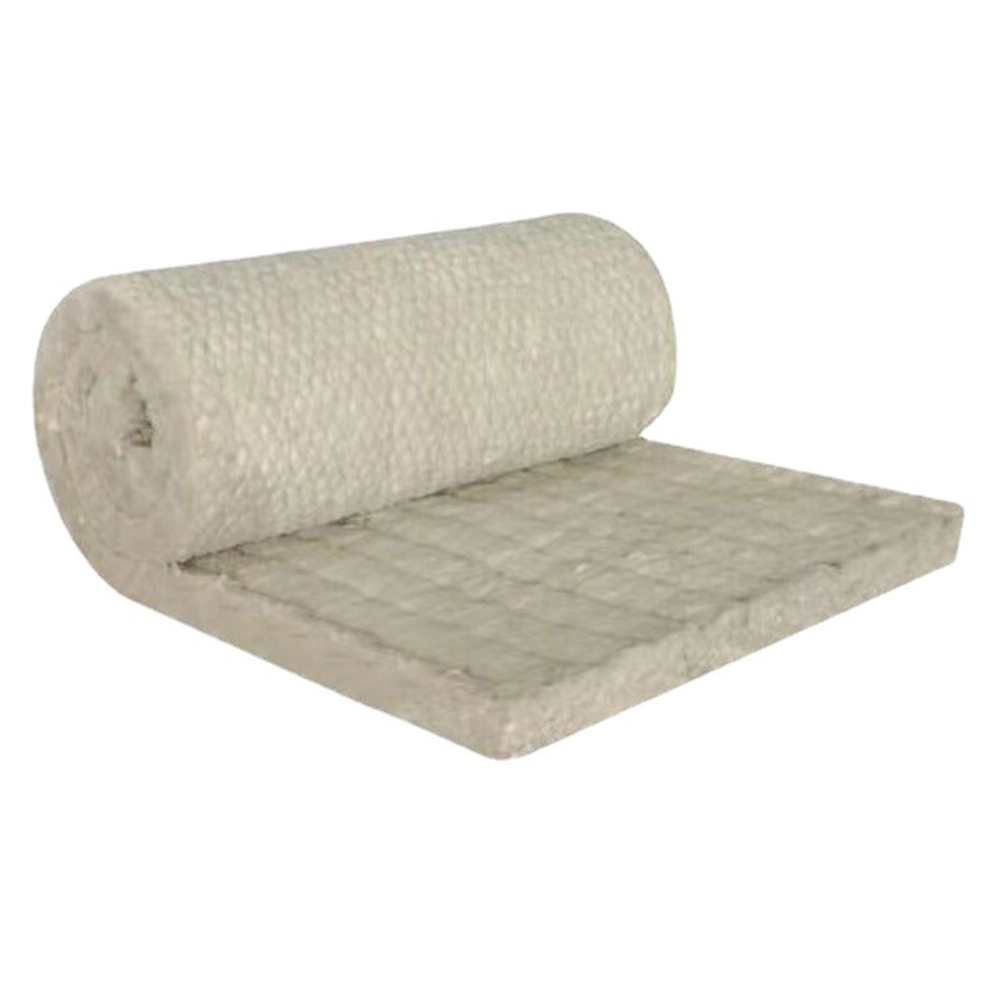
Wholesale Perfect Fire Resistant Performance High Strength Acoustic Mineral Wool Insulation Rock Wool Roll Panel Plain Slab
Rock wool, that is, a kind of exterior insulation material. When the market share of 90% of the organic thermal insulation materials in the stagnant wait-and-see, as a fire rating of A- class exterior insulation inorganic material rock wool has ushered in an unprecedented market opportunity.
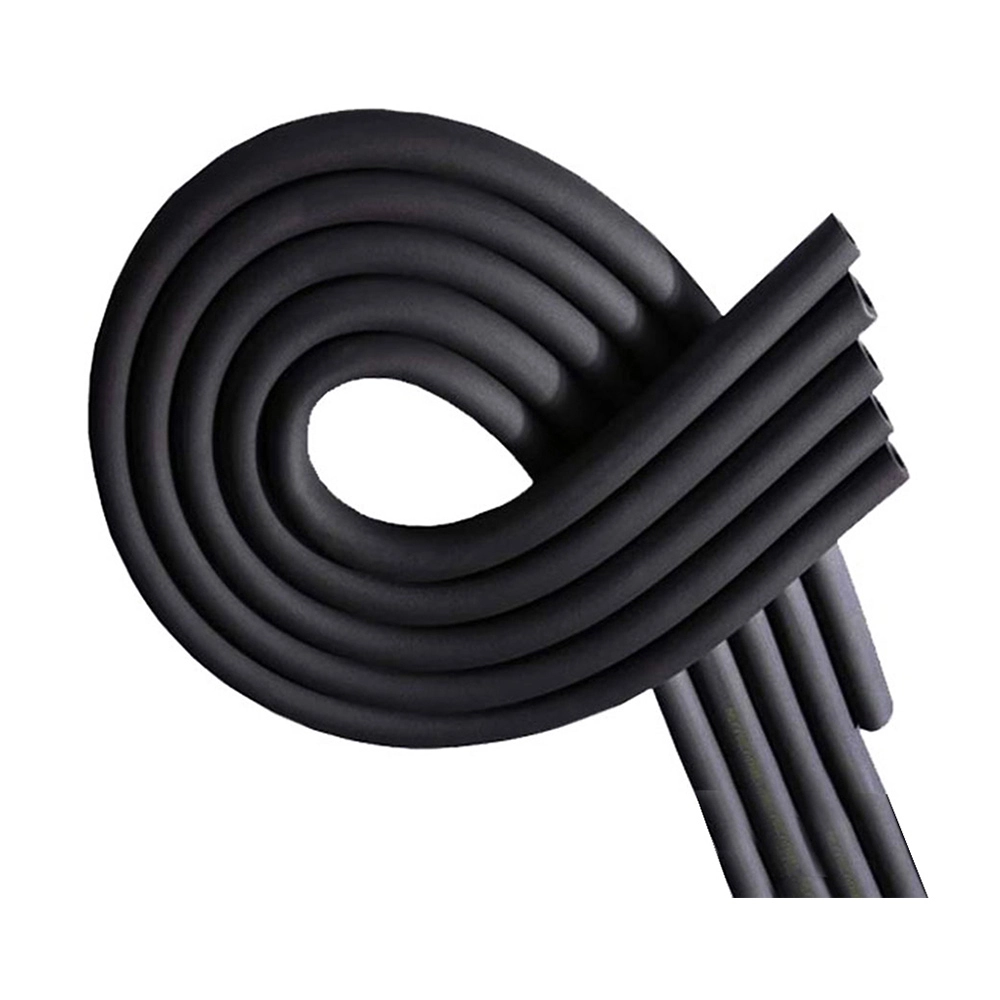
Wholesale Black nitrile rubber foam pipe rubber NBR foam tube rubber foam insulation tube for hvac system
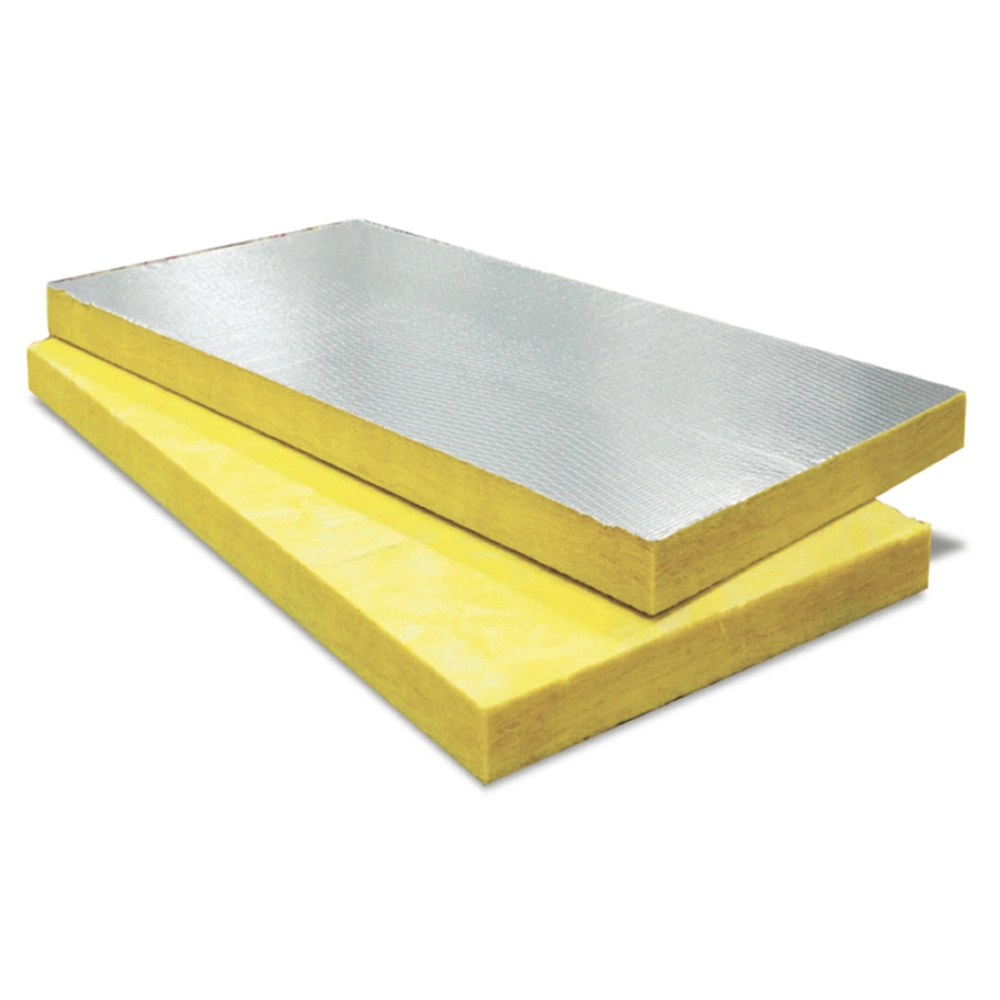
Wholesale Roof And Wall Thermal Heat Insulation 50mm Thickness Aluminum Foil Fiberglass Insulation Panel Board Glass Wool Price
Glass wool is the molten glass fiber, the formation of cotton-like material, chemical composition belongs to the glass category, is a kind of inorganic fiber. With good molding, small volume density, thermal conductivity both, thermal insulation, sound absorption performance is good, corrosion resistance, chemical stability and so on.

Wholesale Perfect Fire Resistant Performance High Strength Acoustic Mineral Wool Insulation Rock Wool Board Panel Plain Slab
Rock wool board, that is, a kind of exterior insulation material. When the market share of 90% of the organic thermal insulation materials in the stagnant wait-and-see, as a fire rating of A-class exterior insulation inorganic material rock wool, has ushered in an unprecedented market opportunity.