Synthetic Rubber Composition
- What is Synthetic Rubber Made Of? – FUNAS
- Understanding the Building Blocks of Synthetic Rubber
- The Key Monomers: The Foundation of Synthetic Rubber
- The Polymerization Process: Creating Long Chains
- Types of Synthetic Rubber Used in Insulation
- The Importance of Additives in Synthetic Rubber
- The Manufacturing Process: From Monomer to Insulation
- Applications of Synthetic Rubber Insulation Materials
- FUNAS: Your Trusted Supplier of Synthetic Rubber Insulation
- Frequently Asked Questions (FAQs)
What is Synthetic Rubber Made Of? – FUNAS
Understanding the Building Blocks of Synthetic Rubber
Synthetic rubber, unlike its natural counterpart, isn't harvested from trees. Instead, it's a manufactured material, carefully crafted from a variety of chemical components. The process begins with monomers, small molecules that link together to form long chains known as polymers. The type and arrangement of these monomers determine the final properties of the synthetic rubber, influencing its flexibility, strength, and resistance to heat, chemicals, and other environmental factors. Understanding this complex interplay is crucial to appreciating the versatility of synthetic rubber insulation materials supplied by FUNAS.
The Key Monomers: The Foundation of Synthetic Rubber
Several crucial monomers contribute to the creation of synthetic rubbers. Some of the most common include:
* Styrene: This monomer is frequently used to create styrene-butadiene rubber (SBR), a widely used synthetic rubber known for its balance of properties. SBR finds applications in numerous industries including the manufacture of insulation products. FUNAS utilizes SBR in various insulation materials due to its cost-effectiveness and robust performance.
* Butadiene: A key component in many synthetic rubbers, including SBR, butadiene contributes to elasticity and resilience. Its presence significantly impacts the overall performance characteristics of the final product, making it essential for applications where flexibility and durability are vital.
* Isoprene: This monomer is used in the production of synthetic polyisoprene, a rubber that closely mimics the properties of natural rubber. This makes it a valuable option in situations requiring high elasticity and low temperature resilience. FUNAS carefully selects its monomers to guarantee optimal performance in diverse climates and applications.
* Nitrile: Acrylonitrile-butadiene rubber (NBR), incorporating nitrile, possesses exceptional resistance to oils and fuels, making it suitable for demanding environments. This makes it a crucial component in specialized insulation solutions provided by FUNAS to the petroleum and petrochemical industries.
* Chloroprene: Polychloroprene (Neoprene) offers outstanding resistance to chemicals, ozone, and weathering. This characteristic makes it a superior choice for insulation in harsh environments, a key area of focus for FUNAS's product development.
The Polymerization Process: Creating Long Chains
The monomers aren't simply mixed together; they undergo a process called polymerization. This involves the controlled linking of monomers to create long, continuous chains, resulting in the formation of the polymer. The polymerization process can be initiated through various methods, including free radical polymerization or anionic polymerization, and the chosen method influences the final properties of the polymer. The precise control of this process is crucial in producing high-quality synthetic rubber, a cornerstone of FUNAS’s manufacturing excellence.
Types of Synthetic Rubber Used in Insulation
Several types of synthetic rubber, each with its unique characteristics, are employed in insulation materials. These include:
* Ethylene Propylene Rubber (EPDM): Known for its excellent weather resistance, ozone resistance, and heat resistance. FUNAS uses EPDM in many insulation products designed for outdoor applications and harsh weather conditions.
* Silicone Rubber: Characterized by extreme temperature resistance, making it ideal for high-temperature insulation applications within industrial settings. FUNAS offers a range of insulation solutions featuring silicone rubber for extreme environments.
* Neoprene (Polychloroprene): Excellent resistance to oils, chemicals, and ozone, frequently used in insulation for applications demanding chemical resistance. FUNAS leverages Neoprene's unique capabilities in its specialized insulation products for diverse industries.
* Nitrile Rubber (NBR): High resistance to oils and fuels, essential for insulation in the petroleum and petrochemical industries. FUNAS utilizes NBR in products specifically designed to withstand the rigors of these demanding sectors.
The Importance of Additives in Synthetic Rubber
The properties of synthetic rubber can be further tailored through the addition of various compounds, such as:
* Fillers: These materials, such as carbon black or silica, are incorporated to improve strength, reduce cost, and modify other properties.
* Plasticizers: These enhance the flexibility and processability of the rubber.
* Antioxidants: These protect the rubber from degradation caused by oxidation.
* Stabilizers: These additives protect against UV degradation and other environmental factors.
FUNAS carefully selects and controls the addition of these compounds to optimize the performance characteristics of its synthetic rubber insulation materials for diverse applications.
The Manufacturing Process: From Monomer to Insulation
The manufacturing process of synthetic rubber is sophisticated and involves multiple stages, including:
1. Monomer Preparation: Purification and preparation of the chosen monomers are crucial for consistent quality.
2. Polymerization: The controlled joining of monomers to form long polymer chains.
3. Compounding: Mixing the polymer with fillers, plasticizers, and other additives.
4. Mixing: Thorough blending of the components to ensure uniform distribution.
5. Fabrication: Shaping the material into the desired form (sheets, tubes, etc.) for insulation purposes.
6. Curing/Vulcanization: A chemical process that cross-links the polymer chains, imparting strength and elasticity to the final product.
7. Quality Control: Rigorous testing ensures adherence to high standards.
Applications of Synthetic Rubber Insulation Materials
Synthetic rubber insulation materials, thanks to their diverse properties, find applications across a wide range of industries:
* Automotive: Insulation in vehicles to reduce noise and heat transfer.
* Construction: Insulation in buildings for thermal and acoustic control.
* Aerospace: Insulation in aircraft and spacecraft to protect sensitive components.
* Refrigeration: Insulation in refrigerators and freezers to maintain low temperatures.
* Oil & Gas: Insulation in pipelines and processing equipment to protect against extreme temperatures and chemicals.
FUNAS's synthetic rubber insulation products cater to these diverse applications, ensuring superior performance and longevity.
FUNAS: Your Trusted Supplier of Synthetic Rubber Insulation
FUNAS, with its expertise in the field of thermal insulation, offers a wide range of high-quality synthetic rubber insulation materials tailored to meet the specific needs of various industries. Our commitment to quality, backed by rigorous testing and certifications, ensures that our products meet the highest standards. We provide customized solutions and brand customization services to perfectly align with our clients’ unique requirements.
Frequently Asked Questions (FAQs)
Q: What are the advantages of using synthetic rubber insulation?
A: Synthetic rubbers offer excellent flexibility, durability, resistance to chemicals and extreme temperatures, and cost-effectiveness compared to some other insulation materials.
Q: What types of certifications does FUNAS hold for its products?
A: FUNAS holds several key certifications, including CCC, CQC, CE, ROHS, CPR, UL, and FM certifications, as well as ISO 9001 and ISO 14001 certifications.
Q: Where are FUNAS products exported?
A: FUNAS exports its products to more than ten countries and regions, including Russia, Indonesia, Myanmar, Vietnam, Tajikistan, and Iraq.
Q: How does FUNAS ensure the quality of its synthetic rubber insulation?
A: FUNAS employs rigorous quality control measures throughout the entire manufacturing process, from raw material selection to final product testing, ensuring adherence to the highest quality standards.
Q: Does FUNAS offer customized solutions?
A: Yes, FUNAS provides brand customization services and caters to specific customer requirements, offering tailored solutions to meet diverse industry needs.
Q: What is the difference between natural and synthetic rubber in insulation?
A: Synthetic rubbers offer more consistent properties, greater resistance to specific chemicals and environmental factors, and often better cost-effectiveness than natural rubber. However, natural rubber can provide superior elasticity in certain applications.
Q: How does the choice of monomer affect the properties of synthetic rubber?
A: Different monomers contribute different properties. For example, butadiene adds elasticity, while nitrile adds oil resistance. The specific monomer mix dictates the final characteristics of the rubber, allowing for tailored performance in diverse applications.
Q: What role do additives play in synthetic rubber insulation?
A: Additives enhance specific properties, such as strength (fillers), flexibility (plasticizers), UV resistance (stabilizers), and longevity (antioxidants). Their precise incorporation is critical for achieving the desired performance in the final product.
Q: Can FUNAS supply synthetic rubber insulation for specialized applications?
A: Yes, FUNAS’s expertise includes developing tailored insulation solutions for specialized applications, even those involving extreme temperatures or aggressive chemical environments. Contact us to discuss your unique requirements.
Q: Where can I learn more about FUNAS products and services?
A: Visit our website or contact us directly. Our team is ready to assist you in selecting the best synthetic rubber insulation solution for your needs.
Basement Insulation Costs Explained by Experts | FUNAS
Extruded Polystyrene Insulation
Understanding Rockwool Composition: A Comprehensive Guide
Comprehensive Guide to Nitrile Rubber Material Properties - FUNAS
service
How does your technical support work?
Our technical support team is available to guide you through every stage of your project—from product selection and design to installation. We provide expert consultation to ensure that you get the best insulation solution for your needs and can assist with troubleshooting if needed.
What is your shipping and delivery process like?
We offer reliable logistics services for insulation material wholesale, both domestically and internationally. Our team ensures secure packaging, timely shipping, and real-time tracking so that your order reaches you in perfect condition and on schedule.
Are your rubber foam products environmentally friendly?
Yes, our insulation products are designed with sustainability in mind. They help reduce energy consumption by minimizing heat loss and gain, and they are made from durable materials that have a long life cycle, reducing the need for frequent replacement.
FAQ
How do I choose the right insulation for my project?
Our team can help you choose the best material for heat insulation based on your specific needs, such as thermal resistance, acoustic properties, and environmental conditions.
Can your insulation products be customized?
Yes, we offer customized solutions for insulation material wholesale to meet the specifications of your project, including custom specifications, sizes, foils and adhesives, colors, etc.
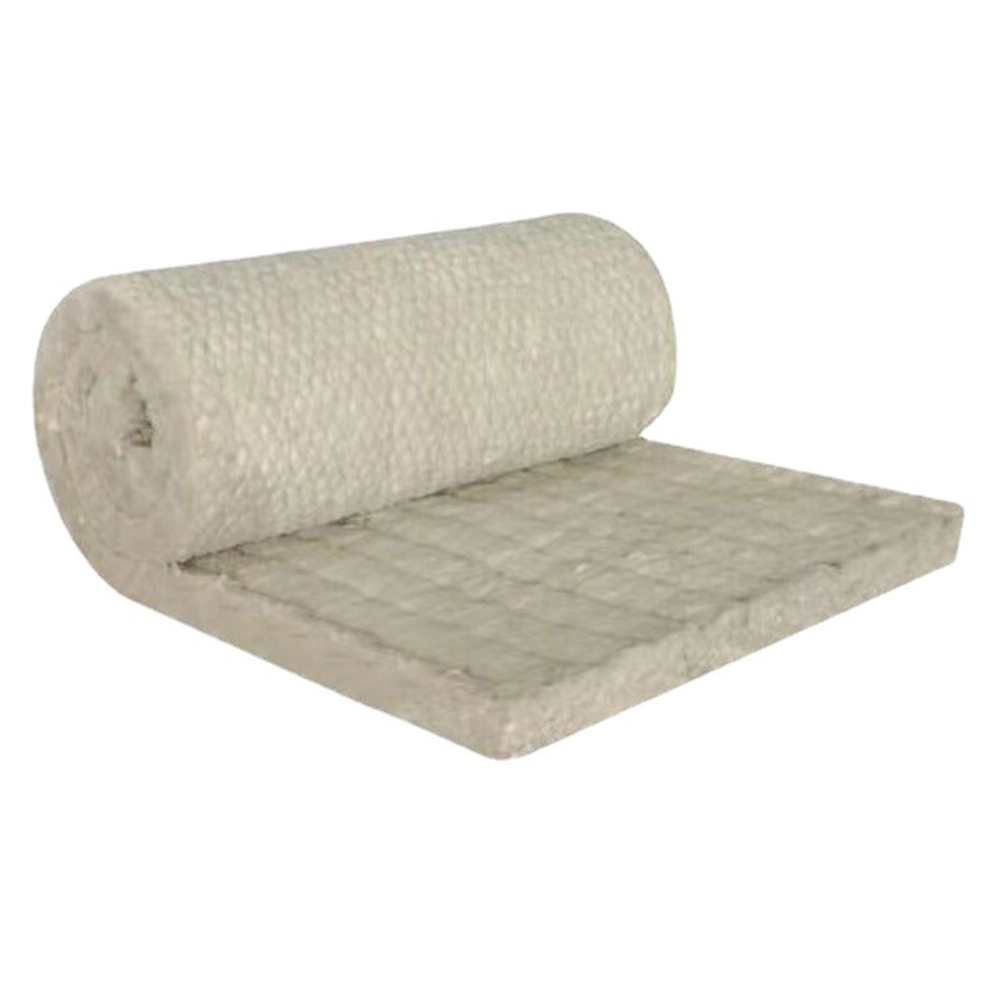
Wholesale Perfect Fire Resistant Performance High Strength Acoustic Mineral Wool Insulation Rock Wool Roll Panel Plain Slab
Rock wool, that is, a kind of exterior insulation material. When the market share of 90% of the organic thermal insulation materials in the stagnant wait-and-see, as a fire rating of A- class exterior insulation inorganic material rock wool has ushered in an unprecedented market opportunity.
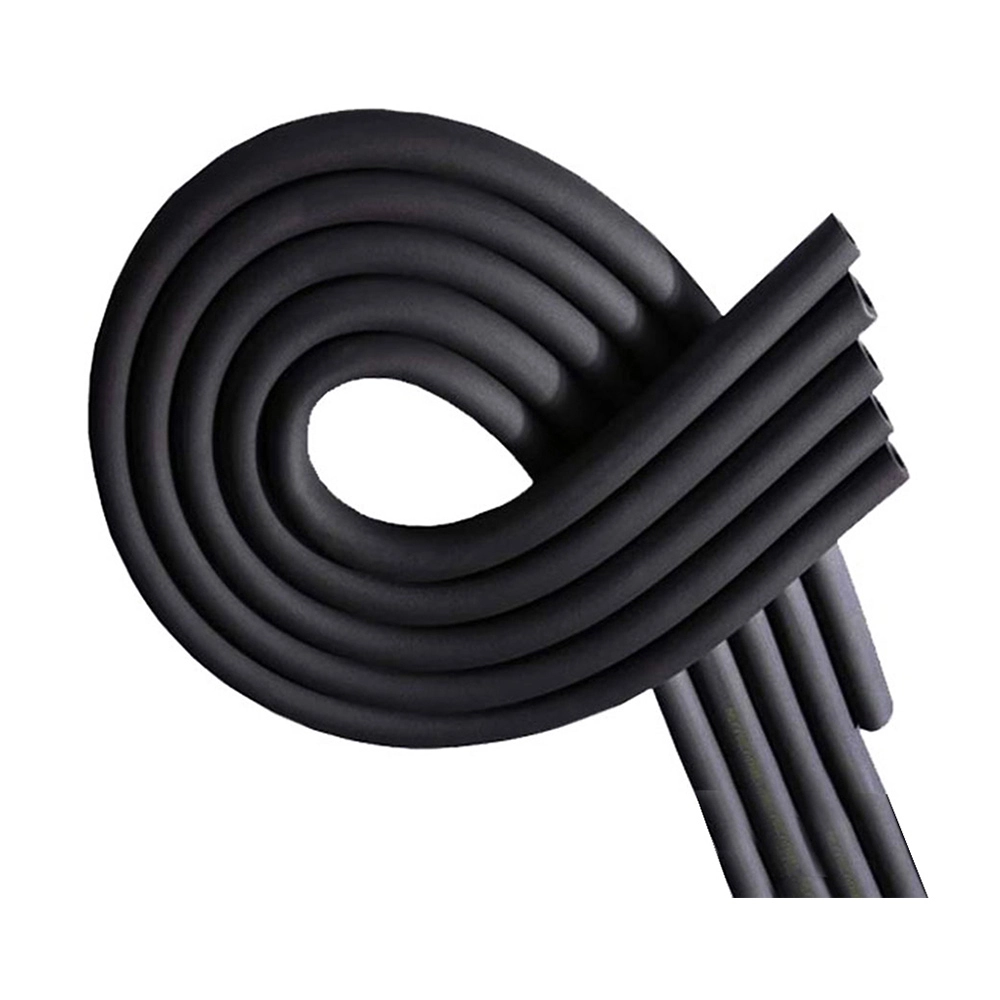
Wholesale Black nitrile rubber foam pipe rubber NBR foam tube rubber foam insulation tube for hvac system
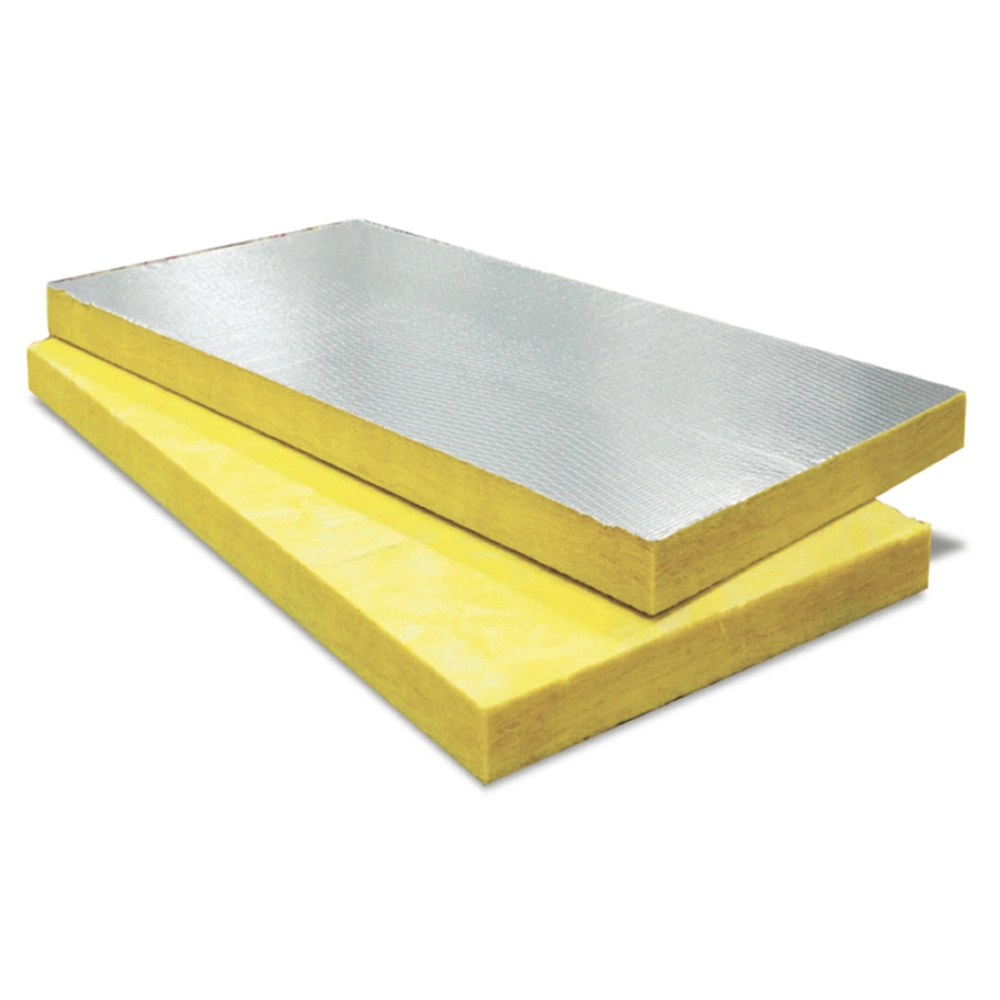
Wholesale Roof And Wall Thermal Heat Insulation 50mm Thickness Aluminum Foil Fiberglass Insulation Panel Board Glass Wool Price
Glass wool is the molten glass fiber, the formation of cotton-like material, chemical composition belongs to the glass category, is a kind of inorganic fiber. With good molding, small volume density, thermal conductivity both, thermal insulation, sound absorption performance is good, corrosion resistance, chemical stability and so on.

Wholesale Perfect Fire Resistant Performance High Strength Acoustic Mineral Wool Insulation Rock Wool Board Panel Plain Slab
Rock wool board, that is, a kind of exterior insulation material. When the market share of 90% of the organic thermal insulation materials in the stagnant wait-and-see, as a fire rating of A-class exterior insulation inorganic material rock wool, has ushered in an unprecedented market opportunity.